The GTA (Greater Toronto Area) is a hotbed for 3PL (3rd Party Logistics) companies who specialize in being the “middle-man” between an online shop’s warehouse and their customers’ homes. Ridiculously large warehouses dot the landscape on both sides of major highways in and out of one of North America’s largest transit hubs. The pandemic made “panic-buying” and online hoarding a reality which put a strain on these 3PLs to maintain delivery windows and inventory. The waves of COVID-19 forced companies to impose stricter safety policies for employees both while physically at work (such as physical distancing) and before coming to work (such as self-screening). These policies caused two big issues: reduced staff due to new capacity limits, and a greater number of employees forced to take time off due to COVID symptoms or exposure. As a result of these issues, we have seen extended delivery times on all online orders; Amazon for instance increased their Prime delivery window from 2-days to 4-days. Companies have been forced to pivot on a weekly basis to keep up with new regulations, which in turn affects the types and quantities of products they’re warehousing as well.
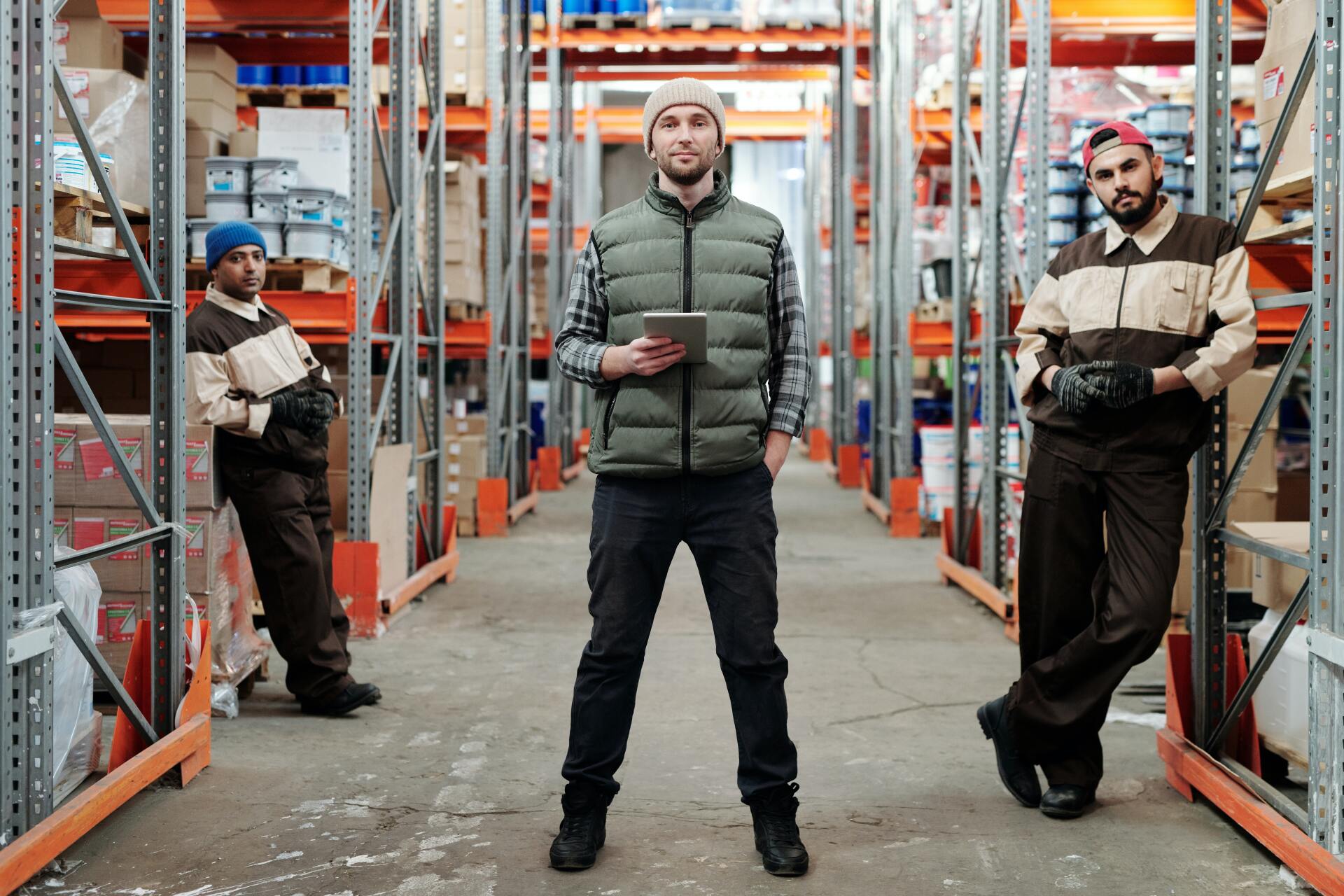
The ease of online purchasing has become so commonplace in 2021 that consumers are unaware of the problems that lie underneath their screens. The world that connects e-commerce to your front door is complex, with orders and deliveries that are carefully navigated by supply chains and logistics companies. These companies are not immune to their own issues, and the pandemic has forced many of them to re-focus and re-adjust their goals and aspirations for the immediate future. Let’s talk about some of the ways that Logistics have had to change to stay efficient with the unexpected arrival of the pandemic.
The peak of pandemic is hopefully behind us globally, but peak season for e-commerce and logistics is here and now. Canadian Thanksgiving is over and Christmas season has officially begun. 2021 labour and supply shortages continue to plague not only the 3PL companies in Canada, but globally as well. If there’s one constant for 2022, it’s that online ordering will not slow down. The supply chain and logistics industry will continue to find new ways to pivot out of the pandemic and find innovative ways to deal with the pains of the previous two years. No one knows what will happen, but at least now they have some practice, and hopefully a better grasp on continuing to move forward.
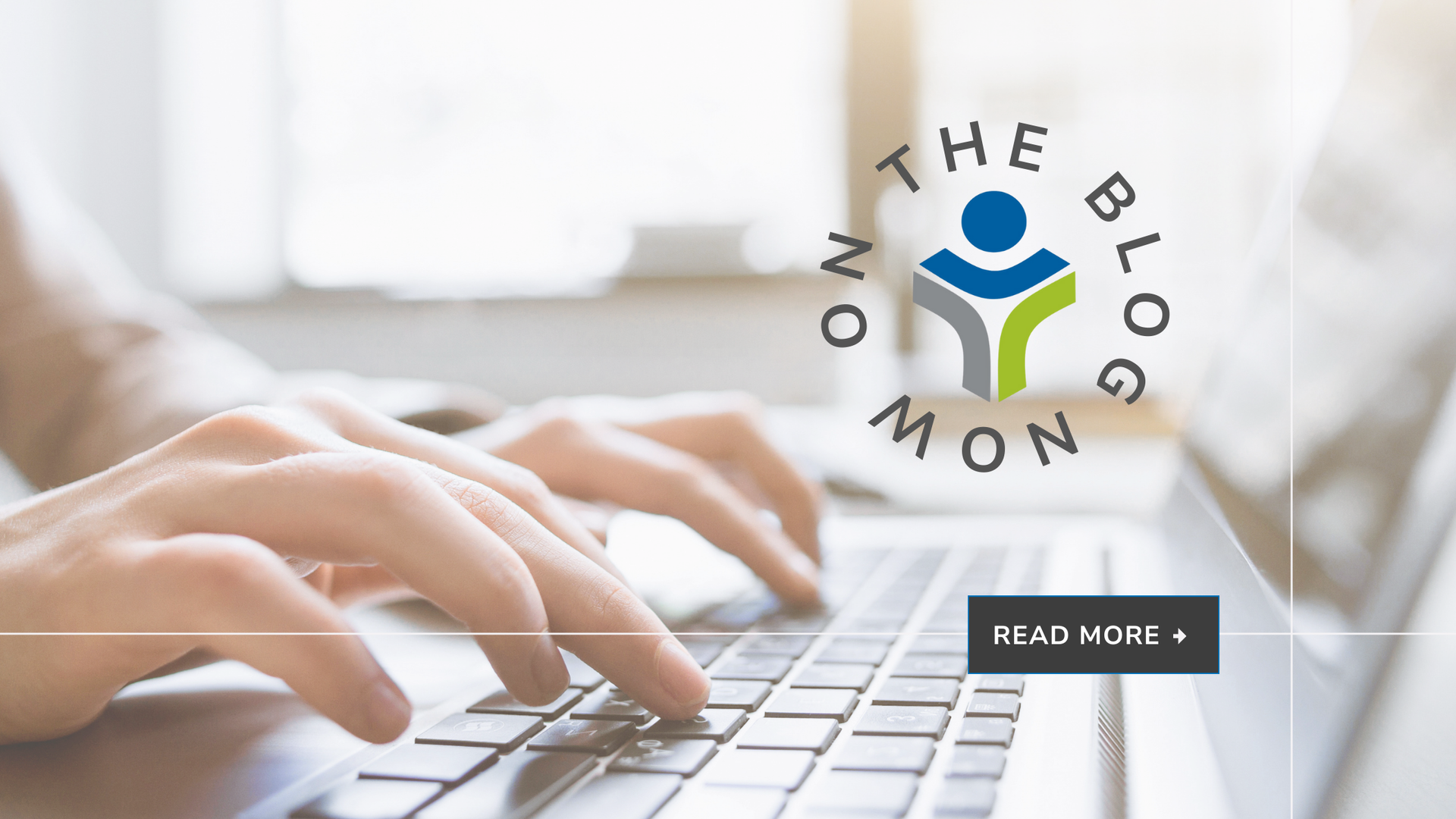